Do you have a formal structure for managing continuous improvements in your business? Whatever your focus, having a structure can improve results.
These six points can help you to get better results. If you find yourself getting stuck with your improvement projects reflect on this list.
Precision
The first point is precision, being precise. Too many projects start off half-cocked. If they actually get completed they are often failures. The results are wrong in the eyes of the stakeholders.
Being clear about the required results is the remedy. Defining what you want to see, experience and have are key.
Do you have a systematic method to define the results you want? Is this an area that you can tighten up on?
Planning
Knowing what needs to happen to achieve your results is another overlooked area. There seems to be a lot of people that assume others know how to get from A to B.
Does this happen in your organisation? Is this expectation present?
If you look at the quality of improvement plans you can see this for yourself. That said, many organisations don’t bother with creating a plan…
‘Winging it’ isn’t a strategy that I recommend. I also don’t recommend planning until your plan is perfect.
What’s the right balance for your organisation?
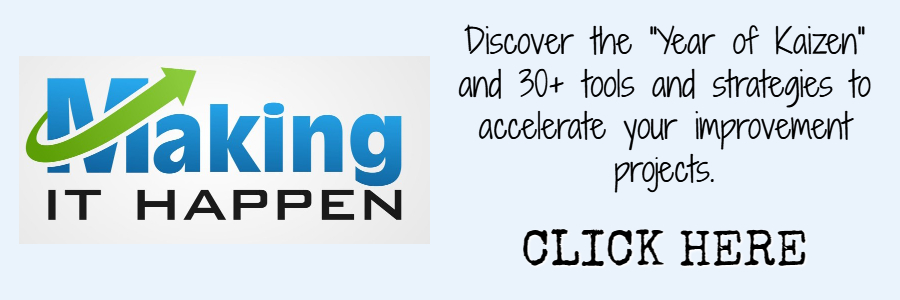
Scheduling
Next up is the ‘when?’ question. When will you undertake the actions from your improvement plan?
Scheduling the tasks isn’t a struggle for many of us. Being realistic, and honest, about when we can perform the tasks is the challenge.
One of the troubles with improvement plans is the lack of an external drive. In some cases there will be an external focus, such as penalties in a formal supply chain. But, other improvements are up to you.
Many organisations watch their improvements slide into oblivion. The projects may start, but they often don’t finish. The results never materialise.
A simple strategy here is to agree a deadline and schedule backwards. Realise that there will never be a great time for your improvements. It might be the case that you need to suck it up and get on with it.
Could your organisation embrace better scheduling of its improvements?
Regular reviews
Setting up an improvement plan is not a sure fire way to improve. Looking at the plan, from time to time, is essential for most of us. ‘Course corrections’ will help keep you on track and achieve results more consistently.
How often you need to review your plans will vary. Some will need daily review, others weekly and others monthly (or less frequent). The level of urgency and risk are usual factors to determine this frequency.
The review doesn’t need to be lengthy. Discussing the obstacles you face, along with an honest appraisal of where you are, should be enough. From here, you can define any corrective actions to get you back on track.
How often do you formally review your improvement plans?
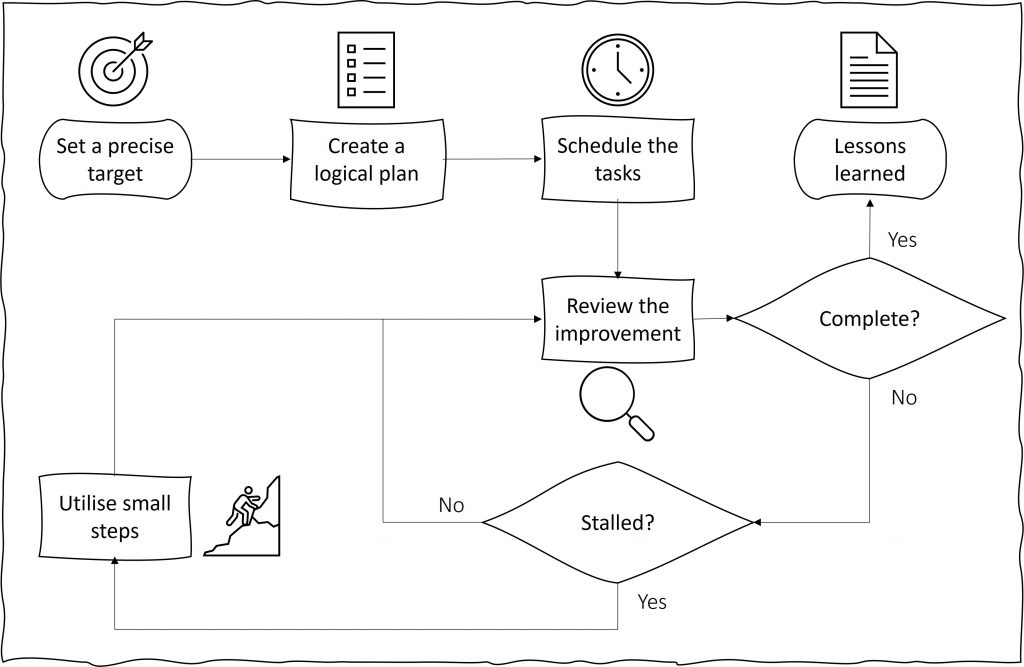
Visibility
Keeping your plans within the minds of all involved is another key consideration. The gusto that comes with the start of a project can soon wane. To keep momentum, it may be necessary to set up in advance ways to keep the project ‘visible’.
The regular reviews are a great way to do this. Finding opportunities to talk about, and promote, the project helps.
You can link the importance of the project to other work activities. With a little bit of thought you can come up with ways to promote the improvement. With enough people talking and thinking about the improvement, results can follow.
Do you need to work on promoting your improvement projects with your teams?
Overcoming inertia
If the progress of your projects slows, having strategies to move them forward are key. Options may include revising priorities, adjusting resources or embracing the Kaizen approach.
Kaizen, in essence, is embracing small steps to create momentum. Small steps build confidence in those undertaking the tasks because they appear do-able. We have so many other tasks to undertake, an improvement project can seem overwhelming. This approach helps to jump start projects.
Do you have enough ‘jump starting’ strategies up your sleeve?
Conclusion
Defining a good improvement plan, and scheduling it, is one part of the improvement jigsaw. Delivering it is another. Whilst I can’t guarantee results from your plans, the above points will help you to deliver your plans.
Reflect on the above points and see if you can improve the results you get for your business.