This is one of the perennial management challenges, isn’t it?
What is merely a small annoyance today, can become tomorrow’s disaster. We’ve all seen this happen.
Let me give you a couple of examples, just in case you need reminding.
- The lights need replaced in a part of the factory, not a problem during Summer months. Then Winter months arrive, and production starts to grind to a halt whilst the team ‘flap’ about trying to source lights and an electrician.
- Organising an additional hire for the project team needs to happen, at some point. Work picks up, everyone says that they don’t have time to deal with this and then customer dissatisfaction grows as projects no longer get delivered on time.
But when does a small task become a crisis?
It certainly isn’t everything that turns into a crisis… but so many things creep there way there that this topic can’t be ignored.
How long does it take to go from niggle to crisis?
Ah, this is the crystal ball question isn’t it?
Some unmet needs will escalate quickly and some will take a long time.
And, whilst some are obvious in terms of what will get nasty soon (think cutting corners with health and safety) some are less obvious.
The key is to have a combination of discussion and measures in place to know when your focus needs to be redirected to deal with specific tasks to prevent the next crisis.
Yes, that’s it, prevention is better than cure.
Who is responsible?
Whilst responsibility certainly becomes higher the further you go up an organisation, everyone has a responsibility to raise their concerns. Perspectives differ, depending on experience, position within the organisation and role. You will see issues that your colleagues will not and vice versa.
For this reason it should be everyone’s responsibility to flag up the small things that need to be dealt with. Sadly, in many organisations, people lower in the organisation do flag up things that are concerning and they don’t get dealt with.
A good example of this is operator maintenance. Let’s say that something isn’t quite right with a piece of equipment when it is checked before use, so the operator reports it to management. The piece of equipment is still functional but not 100% (e.g. a warning light has come on). Management don’t do anything with it and then, one day, the piece of equipment stops working. If the piece of equipment is critical then you get a crisis. If it isn’t, then you might have been lucky and you move on.
What has this got to do with culture?
Letting small issues grow and fester is not what anyone would advise. If it happens enough times then you could argue that this is ‘the way things are done round here’ and suddenly you have a culture of letting things boil over unnecessarily.
If you want to change the culture, then you need to start jumping on these issues in a timely fashion and letting other follow suit. You need to make working the right way normal.
What to do?
If you are reading this and wondering what you can do to change this situation in your organisation then let me share with you a few thoughts:
- Ensure you can measure performance – simple process driven KPIs that can help you to spot when performance is starting to deteriorate.
- Find a way to capture tasks – whiteboard, online ‘to do’ list, paper, anything.
- Find a way to review tasks – keep the task list visible and look at it regularly (no longer than weekly). Think daily meetings.
- Think shelf life and flushing – decide how long a task can stay on your list before you either do it or ditch it.
- Think Kaizen – small steps can gather momentum and overcome a feeling of overwhelm. Nibble away rather than do nothing and keep progress moving (even if it is a tiny gesture or simply making a decision).
- Turn fixes into routines – prevent reoccurrence by spotting the routines that your business needs and implement accordingly. Or, put another way extend management appropriately.
How do you spot a crisis task?
The simplest way is to talk to your team to start thinking about concerns.
If something isn’t right then raise it as a concern.
The simple framework for handling concerns is the ‘concern – cause – countermeasure‘ method (also known as the CCC or 3C method).
In essence, you capture concerns and at a later point (you determine when) you consider the true root cause of the concern and then an effective countermeasure.
The collection of your countermeasures is simply your improvement action plan.
Some of your concerns will want to be prioritised and some can wait a while.
You will know the difference, the key is to raise concerns and not let the issues get to the point of crisis.
Do you want some tools to help you prevent future crises?
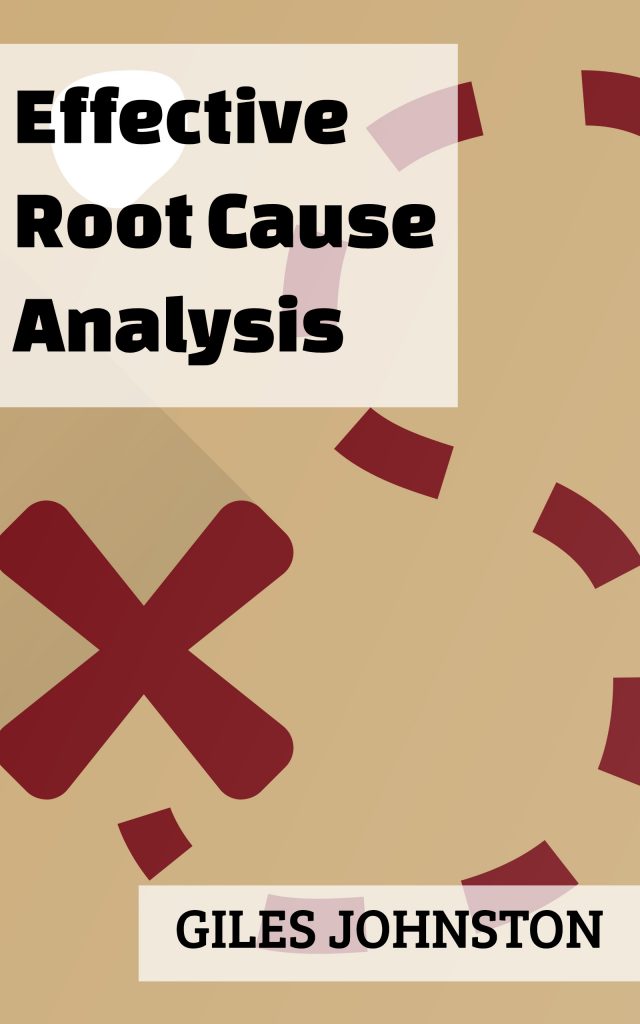
Root Cause Analysis
A practical book that can help you get the most out of root cause analysis (available from Amazon and iTunes).
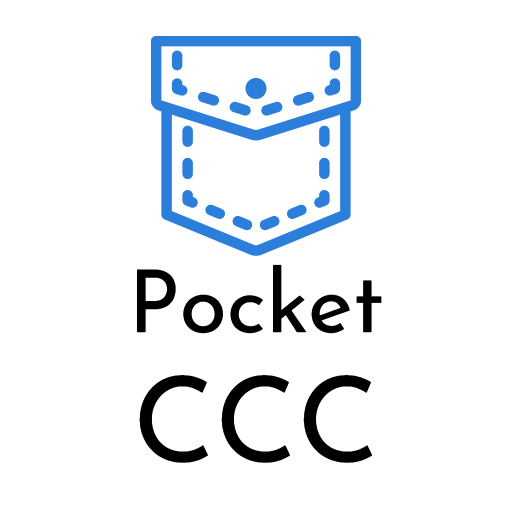
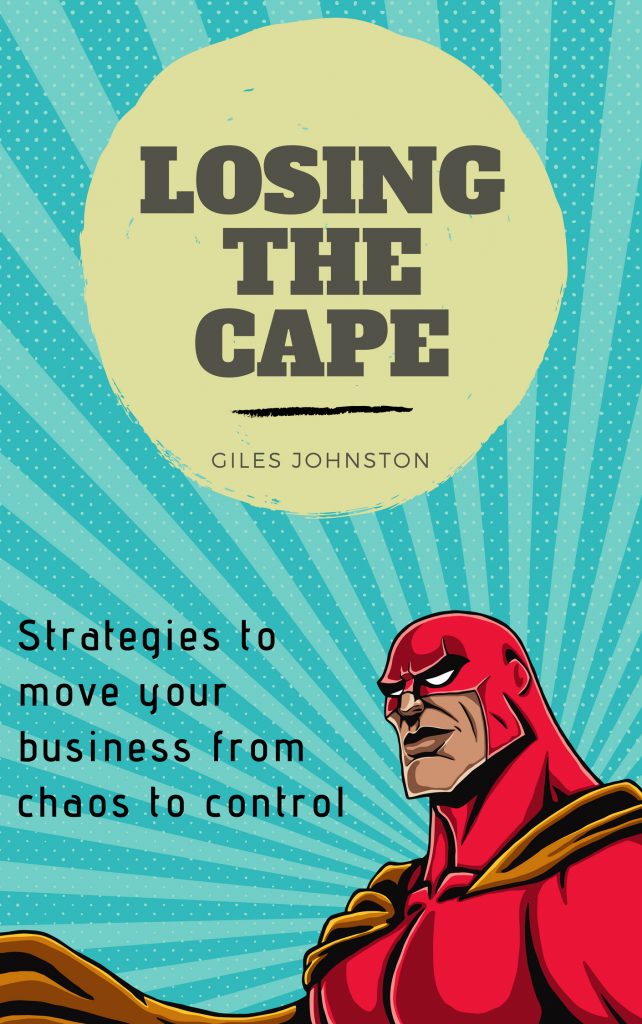
Losing the Cape
Another book, to help you spot where crises can come from and reduce your reliance on the need for ‘superheroes’ in your business.
I hope that you can steer your team into being open and honest about the concerns they have in the business and then tie them into a process that allows you to handle them efficiently and effectively.
Being proactive with concerns is not only a great way to improve your business’ performance but also a great way to stop losing time to crises that suck time and energy out of you and your business.
What are you concerned about?
You might as well start now.